OEE คืออะไร
OEE ( Overall Equipment Effectiveness ) เป็นการวัดประสิทธิภาพของการผลิต โดยส่วนมากแล้วจะใช้วัดในส่วนของการทำงานของเครื่องจักร โดยใช้เพื่อเป็นการประเมินถึงประสิทธิภาพของการผลิต ว่ามีคุณภาพมากน้อยเพียงใด โดยมีคะแนนเต็มอยู่ที่ 100% หากให้ยกตัวอย่างที่เข้าใจง่ายที่สุด ก็เปรียบดั่งการวัดผลของคุณภาพการเรียน โดยจะมีการให้คะแนนเป็นเกรดจาก 100% ว่าสามารถทำได้มากน้อยเพียงใด
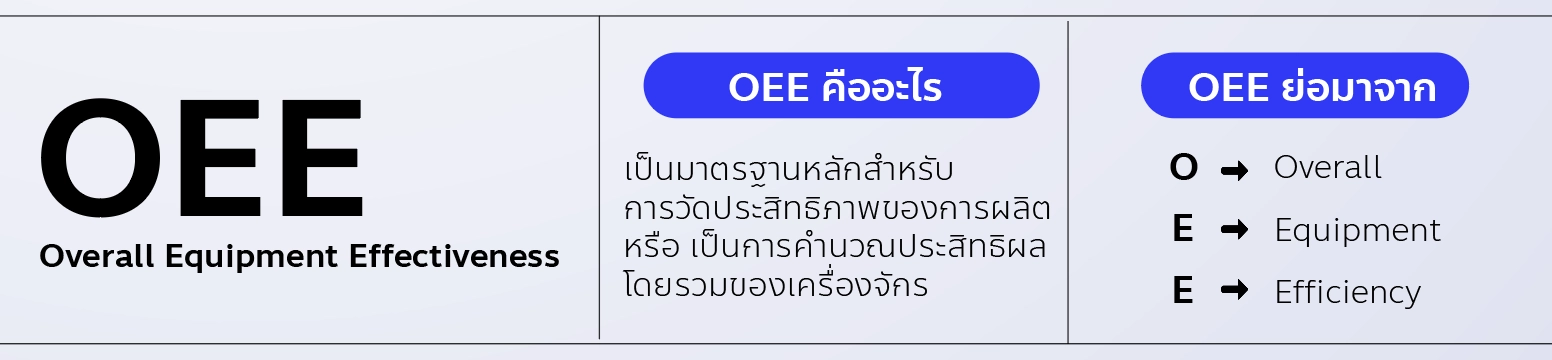
ยิ่งผลการวัดออกมาใกล้เคียง 100% มากเท่าไหร่ นั่นก็เป็นการบ่งบอกอย่างชัดเจนว่าในกระบวนการผลิตนั้น ทุกอย่างเป็นไปได้ด้วยดี แต่หากมีผลการตรวจสอบที่น้อยลงมา ก็สามารถตามหาต้นตอของปัญหาเหล่านั้นได้ ซึ่งเป็นส่วนสำคัญที่ทำให้เห็นประสิทธิภาพการทำงานของกระบวนการผลิต ว่ามีประสิทธิภาพมากน้อยแค่ไหน มีสิ่งใดที่ควรต้องแก้ไขบ้างนั่นเอง
Quick Suggest
หากสนใจเรียนรู้เพิ่มเติม ขอแนะนำบทความ
วัตถุประสงค์ของการใช้งาน OEE
การวัดผลด้วยวิธี OEE เป็นวิธีที่ดีที่สุด สำหรับการทำให้คุณสามารถเห็นภาพรวม ของประสิทธิภาพการผลิตขององค์กร ส่งผลให้สามารถประเมินกำลังการผลิตได้อย่างแม่นยำ ตลอดไปจนถึงการมองหาวิธีแก้ไขปัญหา
ในกรณีผลการวัดค่านั้นออกมาได้น้อยกว่าที่คาดการณ์เอาไว้ เนื่องจากในขั้นตอนการคำนวณ จะมีการนำสถิติทั้งหมดของการผลิต ไม่ว่าจะเป็น ระยะเวลาการทำงาน คุณภาพของสินค้า และ ข้อผิดพลาดที่ทำให้ต้องหยุดการทำงาน และตัวแปรอื่น ๆ ที่ช่วยให้เล็งเห็นแนวทางการแก้ปัญหาที่ตรงจุดมากที่สุด
โดยเราได้สรุปมาให้เรียบร้อยแล้วว่า เพราะอะไรองค์กรของคุณควรวัดค่า Overall Equipment Effectiveness
ปรับปรุงประสิทธิภาพ
การตรวจสอบ OEE ทำให้สามารถระบุส่วนที่ทำให้การผลิตที่ไม่มีประสิทธิภาพเท่าที่ควร และให้ข้อมูลเชิงลึกเพื่อนำไปปรับปรุงแก้ไขได้อย่างตรงจุด เมื่อผลการประเมินกลับมาได้ดังที่ต้องการ นั่นหมายความถึงการผลิตที่มีประสิทธิภาพมากยิ่งขึ้นอีกด้วย
ลดต้นทุน
เมื่อเห็นจุดที่ควรแก้ไขอย่างชัดเจน ก็จะทราบสาเหตุของการหยุดทำงานโดยไม่จำเป็น หากแก้ไขได้อย่างตรงจุด จะสามารถลดต้นทุนการผลิตที่สูญเสียไปได้ พร้อมกับประหยัดงบประมาณการบำรุงรักษาอีกด้วย
ใช้งานอุปกรณ์ให้เกิดประโยชน์สูงสุด
ในกรณีที่อุปกรณ์ที่ใช้งานเป็นเครื่องจักร การประเมิน OEE ช่วยให้สามารถใช้งานศักยภาพของเครื่องจักรได้สูงที่สุด เพื่อให้ง่ายต่อการกำหนดแนวทางการใช้งาน การซ่อมบำรุง และลดระยะเวลาว่างที่เสียไปโดยใช่เหตุ
ความเป็นสากล
เป็นการประเมินคุณภาพที่ใช้กันทั่วโลก ผลของการประเมิน OEE เป็นการวัดที่ใช้กันอย่างแพร่หลายทั่วทุกมุมโลก ดังนั้นค่าที่วัดได้สามารถนำไปใช้เพื่อสื่อสารกับทีมงาน ซัพพลายเออร์ ตลอดจนถึงการนำไปเสนอลูกค้า เพื่อแสดงออกถึงกำลังการผลิตขององค์กร ว่ามีประสิทธิภาพมากเพียงใด
ส่วนประกอบของ OEE
Overall Equipment Effectiveness เป็นดัชนีการผลิตที่ดีที่สุด สำหรับการนำมาวินิจฉัยสาเหตุของการสูญเสีย การวัดค่านั้นจะถูกวัดจากระยะเวลาการผลิตที่วางแผนเอาไว้ หักลบช่วงเวลาที่หยุดการทำงานที่ตั้งใจออกไปแล้ว เช่น วันหยุด, ช่วงเวลาพัก, การซ่อมบำรุงเครื่องจักร เป็นต้น หลังจากได้แผนการทำงานที่ต้องการแล้วนั่นถือว่าเป็นระยะเวลาการผลิตทั้งหมด ต่อจากนั้นเราก็จะมาประเมินกันต่อกับอีก 3 ปัจจัยหลักของการประเมิน OEE ซึ่งนั่นก็คือ
1. ความพร้อมใช้งาน (Availability)
ความพร้อมใช้งานคือ “การผลิตตามแผนงานที่กำหนดเอาไว้” ซึ่งปัญหาที่จะถูกประเมินจะเป็นปัญหาที่เกิดขึ้นกะทันหัน ไม่ได้อยู่ในแผนการที่วางแผนเอาไว้ เช่น เครื่องจักรเกิดการชำรุด ทำให้ต้องหยุดการผลิตชั่วคราว หรือวัตถุดิบที่จะต้องใช้ในการผลิตไม่เพียงพอต่อความต้องการ ในกรณีนี้หากเกิดการหยุดการทำงาน แต่เป็นไปตามแผนที่วางเอาไว้ เช่นการหยุดพักเครื่องจักรตามวงรอบ การซ่อมบำรุง จะไม่ถูกนำไปหักลบในขั้นตอนการประเมิน OEE หากในปัจจัยนี้ประเมินได้ 100% เต็ม แสดงว่ามีการทำงานตลอดระยะเวลา โดยไม่มีการสะดุดเลยแม้แต่นิดเดียว ค่าที่วัดได้จะถูกเรียกว่า “อัตราการเดินเครื่อง”
2. ประสิทธิภาพการทำงาน (Performance)
ประสิทธิภาพการทำงานของ OEE จะถูกประเมินจากการเก็บสถิติเอาไว้ มีเป้าหมายอย่างชัดเจนที่จะตั้งมาตรฐานของการทำงานตามปกติ และจะมองหาระยะเวลาที่ต้องสูญเสียไปจากการทำงานที่เพิ่มมากขึ้นมาอย่างสูญเปล่า ยกตัวอย่างเช่น ตามปกติแล้วโรงงานมีกำลังการผลิตชิ้นงานอยู่ที่ 60 ชิ้น ใน 1 ชั่วโมง นั่นถือเป็น “ค่ามาตรฐาน” หากในการผลิตครั้งต่อไป การผลิตชิ้นงาน 60 ชิ้น หากใช้ระยะเวลามากกว่า 1 ชั่วโมง ส่วนต่างในระยะเวลาที่เกินมาก็จะถูกนำมาหักลบเพื่อประเมินหาระยะเวลาที่สูญเสียไป โดยการหักนั้นจะมีทั้งในรูปแบบ ซึ่งจะมีการหักจาก “Slow Cycles” คือการทำนานกว่าปกติเล็กน้อย และ “Small Stop” เป็นการหยุดการผลิตในช่วงสั้น ๆ หลังจากหักลบระยะเวลาที่สูญเสียไปเสร็จเรียบร้อยแล้ว คุณจะได้ “ประสิทธิภาพการเดินเครื่อง”
3. คุณภาพของการทำงาน (Quality)
ส่วนสุดท้ายของการประเมิน Overall Equipment Effectiveness คือคุณภาพของชิ้นงาน โดยจะนับจากชิ้นงานทั้งหมดที่ผลิตออกมา หักลบกับชิ้นงานที่ไม่ผ่านการตรวจสอบคุณภาพ หรือเรียกง่าย ๆ ว่า “สินค้าที่เสียหาย” นั่นเอง ในการทำงานที่ได้คุณภาพ 100% บ่งบอกถึงคุณภาพการผลิตที่ไร้ซึ่งข้อผิดพลาด สินค้าทุกชิ้นที่ผ่านกระบวนการผลิตมีคุณภาพอันไร้ที่ติ สำหรับการคำนวณ OEE จะนำเอา สินค้าที่ผลิตได้ทั้งหมด หักลบด้วยสินค้าที่เสียหาย จนได้เป็น “อัตราคุณภาพ” นั่นเอง
การคำนวณ OEE
การคำนวณ Overall Equipment Effectiveness นั้นมีกรรมวิธีที่ง่ายเป็นอย่างมาก มีวิธีคิดเพียงนำเอา “อัตราการเดินเครื่อง” x “ประสิทธิภาพการเดินเครื่อง” x “อัตราคุณภาพ” เพียงเท่านี้ก็จะได้ค่า OEE สำหรับการประเมินออกมาเป็น % เป็นที่เรียบร้อย โดยต่อจากนี้เราจะขอยกตัวอย่าง การประเมินคุณภาพการผลิต ของบริษัท A ดังเนื้อหาต่อจากนี้
ตัวอย่าง
“ บริษัท A มีไลน์ผลิตที่มีเครื่องจักรสามารถทำงานได้อยู่ที่ 50 ชั่วโมงต่อสัปดาห์ มีการวางแผนเพื่อให้มีการพักเครื่องจักรตามแผนงานเอาไว้ที่ 5 ชั่วโมง ในสัปดาห์หนึ่ง เกิดการสูญเสียเวลาจากการหยุดการผลิตไป 3 ชั่วโมง กำลังผลิตของโรงงานนี้อยู่ที่ 500 ชิ้น ต่อ 40 ชั่วโมง โดยในสัปดาห์นี้สามารถดำเนินการโดยใช้ระยะเวลาไป 43 ชั่วโมง ผลิตสินค้าได้จำนวน 500 ชิ้น สินค้าเสียหายจำนวน 50 ชิ้น ”
ถ้าหากจะคิดเป็น % ต้อง x100 ครับ แต่ถ้าใส่ใน Excel แล้วทำเป็น % โดย Excel จะคำนวณให้อัตโนมัติครับ
วิธีคำนวณ “อัตราการเดินเครื่อง”
หา “เวลารับภาระงาน” = ระยะเวลาทำงานทั้งหมด – การหยุดตามแผน
= 50 – 5
= เวลารับภาระงานคือ 45 ชั่วโมง
หา “อัตราการเดินเครื่อง” = ( เวลารับภาระงาน – เวลาการหยุดเครื่องจักร ) / เวลารับภาระงาน
= ( 45 – 3 ) / 45
= อัตราการเดินเครื่องคือ 93%
วิธีคำนวณ “ประสิทธิภาพการเดินเครื่อง”
หา “ระยะเวลาที่สูญเสียความเร็ว” = เวลาที่ทำได้ – ระยะเวลามาตรฐาน
= 43 – 40
= ระยะเวลาที่สูญเสียความเร็วคือ 3 ชั่วโมง
หา “ประสิทธิภาพการเดินเครื่อง” = ( ระยะเวลามาตรฐาน – ระยะเวลาที่สูญเสียความเร็ว ) / ระยะเวลามาตรฐาน
= ( 40 – 3 ) / 40
= อัตราการเดินเครื่องคือ 92.5%
วิธีคำนวณ “อัตราคุณภาพ”
หา “อัตราคุณภาพ” = ( จำนวนสินค้าที่ผลิตได้ทั้งหมด – สินค้าที่เสียหาย) / จำนวนสินค้าที่ผลิตได้ทั้งหมด
= ( 500 – 50 ) / 500
= อัตราการเดินเครื่องคือ 90%
วิธีคำนวณ OEE
จากการวิเคราะห์ข้อมูลทั้ง 3 แหล่งเป็นที่เรียบร้อยแล้ว เราจะได้ข้อมูลที่ต้องการเพื่อนำมาคำนวณในวิธีคิดที่ว่า
“อัตราการเดินเครื่อง x ประสิทธิภาพการเดินเครื่อง x อัตราคุณภาพ”
“ 93% x 92.5% x 90% ”
= ผลลัพธ์ของการประเมิน Overall Equipment Effectiveness ที่ได้ของบริษัท A ในช่วงสัปดาห์นี้คือ 77.4%
วิธีเพิ่ม OEE ให้สูงขึ้น
หากประเมิน Overall Equipment Effectiveness แล้วผลออกมาไม่ได้ตามมาตรฐานที่ตั้งเอาไว้ หรือต้องการมาตรฐานที่สูงมากกว่าเดิม การแก้ปัญหานั้นจะต้องแก้ที่สาเหตุของความสูญเสียที่เสียไป โดยเราจะแก้ไขแบบ Case by case ตาม 3 ปัจจัยหลักของการประเมิน OEE ดังต่อไปนี้
ความพร้อมในการใช้งาน
หากปัญหาเกิดจากความพร้อมใช้งาน อาจต้องมองหาระยะเวลาที่สูญเสียไปโดยไร้ประโยชน์ รวมไปถึงลดระยะเวลาการหยุดเครื่องจักรให้น้อยลง เตรียมวัตถุดิบให้พร้อมต่อการผลิตอยู่เสมอ เป็นต้น
ประสิทธิภาพการทำงาน
หากปัญหาเกิดจากประสิทธิภาพการทำงาน ปัญหาที่มักเกิดขึ้นในปัจจัยนี้ มักมาจากการสึกหรอของชิ้นส่วนบางอย่างในเครื่องจักร วัตถุดิบที่มีคุณภาพต่ำกว่ามากตราฐาน รวมไปถึงการทำงานผิดปกติของเครื่องจักร การแก้ไขปัญหาคือต้องหมั่นดูแลรักษาเครื่องจักร ให้อยู่ในคุณภาพที่พร้อมใช้งานอยู่เสมอ
คุณภาพการทำงาน
หากปัญหาเกิดจากคุณภาพของการทำงาน ข้อผิดพลาดในจุดนี้ส่วนมากแล้วมักเกิดจากความผิดพลาดของกระบวนการ เช่น ปัญหาเกี่ยวกับการป้อนชิ้นงาน วัตถุดิบไม่เป็นตามที่ต้องการ ความผิดปกติของเครื่องจักร การแก้ปัญหาคือการตรวจสอบปัญหาที่เกิดขึ้น และแก้ไขให้ได้โดยเร็ว
ประโยชน์ของ OEE ในอุตสาหกรรม
ประโยชน์อันเด่นชัดของการประเมิน Overall Equipment Effectiveness ในงานอุตสาหกรรมคือ “ได้ข้อมูลเชิงลึกของคุณภาพการผลิต” ซึ่งข้อมูลเชิงลึกที่ได้มาจะมีตั้ง คุณภาพการผลิต ระยะเวลาการทำงาน ระยะเวลาที่สูญเสียไป กำลังการผลิต และ ความแม่นยำของการผลิต ทุกสิ่งที่กล่าวไปข้างต้นสามารถบ่งบอกได้ถึงประสิทธิภาพของการดำเนินงาน หากในส่วนไหนมีข้อผิดพลาดก็สามารถมองหาสาเหตุและแก้ไขได้ทันที การปล่อยให้ค่าของ OEE ต่ำลงเรื่อย ๆ ไม่ส่งผลดีต่อองค์กรเป็นอย่างมาก นอกจากทำให้สิ้นเปลืองทรัพยากรแล้ว ยังส่งผลเสียต่อการยื่นผลการประเมิน เพื่อดึงดูดให้ลูกค้าใหม่เข้ามาใช้บริการอีกด้วย
จุดควรระวังของการตรวจสอบ OEE
แม้ว่าการประเมิน OEE จะมีผลดีอย่างมากต่อองค์กร แต่หากการประเมินครั้งนั้นมีข้อผิดพลาดบางอย่าง ซึ่งทำให้ค่าที่ได้มานั้นไม่แม่นยำตามที่ควรจะเป็น อาจทำให้เกิดผลเสียต่อการประเมินผลได้ ในเนื้อหาต่อจากนี้เราจะมาแนะนำจุดที่มักเกิดข้อผิดพลาดอยู่บ่อย ๆ พร้อมแนะนำวิธีการแก้ไขและป้องกันปัญหาเบื้องต้น
1. ตรวจสอบข้อมูล
การจดบันทึกสถิติต่าง ๆ บางครั้งอาจมีตัวแปรที่ทำให้เกิดความคลาดเคลื่อนของตัวเลข ดังนั้นก่อนนำตัวเลขมาคำนวณ จะต้องมั่นใจว่าข้อมูลทั้งหมดนั้นถูกต้อง 100%
2. ตรวจสอบหน่วย
หน่วยที่ใช้จะต้องเป็นหน่วยเดียวกัน ไม่ว่าจะเป็นในส่วนของ ปริมาณ เวลา ชิ้นงาน เป็นต้น หากใช้หน่วยของการคำนวณที่แตกต่างกัน อาจทำให้ค่าที่ได้มานั้นผิดเพี้ยนไปในทันที ส่วนนี้ต้องระวังเป็นอย่างมาก
3. Human Error
การผิดพลาดจาก Human Error เนื่องจากตัวเลขบางอย่าง ไม่สามารถใช้เครื่องจักรนับได้ อาจจะต้องใช้มนุษย์เป็นผู้ตรวจสอบ ดังนั้นในส่วนนี้อาจเกิดข้อผิดพลาดได้ ทางที่ดีคือต้องกำชับผู้ตรวจนับ จะต้องจดบันทึกให้แม่นยำมากที่สุด
OEE กับ Lean Manufacturing
Lean Manufacturing (ระบบการผลิตแบบลีน) คือกระบวนการที่ทำให้การดำเนินงานนั้นเกิดประสิทธิภาพสูงที่สุด ซึ่ง Overall Equipment Effectiveness ก็เป็นส่วนหนึ่งของกระบวนการนั้น กระบวนการผลิตเป็นส่วนสำคัญที่สุด สามารถตัดสินได้เลยว่าองค์กรนั้น ๆ จะมีผลกำไรมากน้อยเพียงใดในไตรมาสนั้น ๆ ดังนั้นการนำเอาระบบการผลิตแบบลีนมาใช้ จะส่งผลดีเป็นอย่างมากต่อการผลิต โดยแนวคิดนั้นก็สุดแสนจะเรียบง่าย คือการ “ลดความสูญเปล่าให้ได้มากที่สุด” ไม่ว่าจะเป็นการสูญเปล่าจากการผลิตที่ไม่มีคุณภาพ การสูญเปล่าจากการผลิตสินค้ามากเกินไป การสูญเปล่าจากการรอคอย การสูญเปล่าจากการขนย้ายที่ไม่มีประสิทธิภาพ เป็นต้น
การนำ OEE ไปใช้ในการบริหารจัดการโรงงาน
หากโรงงานของคุณกำลังประสบปัญหา กระบวนการผลิตที่ยังทำยอดได้ไม่เข้าเป้า การนำเอากระบวนการ Overall Equipment Effectiveness เข้าไปปรับใช้เพื่อบริการจัดการในโรงงาน เป็นอีกหนึ่งวิธีแก้ไขปัญหาที่เห็นผลได้อย่างรวดเร็ว เนื่องจากคุณจะได้พบกับต้นตอของสาเหตุ ที่ทำให้ยอดการผลิตไม่เข้าเป้า ได้เห็นถึงความสูญเปล่าที่เสียไปโดยไม่ได้อะไรกลับคืนมา และได้แนวคิดการปรับปรุงกระบวนการผลิตให้สามารถทำงานได้อย่างเต็มประสิทธิภาพมากยิ่งขึ้น ซึ่งทั้งหมดนั้นจะเป็นไปไม่ได้เลย หากคุณยังขาด “Planned Production Time” ที่ดีพอ ดังนั้นควรนำเอาหลักการ OEE นำไปคำนวณหาแผนการผลิตที่เหมาะสมมากที่สุด สุดท้ายแล้วคุณจะได้รับผลผลิตตามที่คุณนั้นต้องการอย่างแน่นอน
ความสำคัญของ OEE ในการวัดประสิทธิภาพการผลิต
1. เพิ่มประสิทธิภาพการผลิต
เพิ่มประสิทธิภาพของการผลิต ให้ได้สินค้าที่มีคุณภาพ และใช้ระยะเวลาการผลิตได้คุ้มค่ามากที่สุด
2. ลดความผิดพลาด
ลดจำนวนสินค้าที่มีข้อผิดพลาดให้น้อยลง ช่วยให้ประหยัดเวลาการแก้ไขชิ้นงานนั้น ๆ
3. เพิ่มมูลค่าการผลิต
ช่วยเพิ่มมูลค่าการผลิตให้มากขึ้น หากประเมิน Overall Equipment Effectiveness อย่างถูกต้อง พร้อมกับแก้ไขปัญหาอย่างตรงจุด มั่นใจได้เลยว่าโรงงานของคุณจะทำกำไรได้มากขึ้นอย่างแน่นอน
4. แก้ไขได้รวดเร็ว
สามารถรับรู้ข้อผิดพลาด และปรับปรุงแก้ไขได้อย่างต่อเนื่อง ด้วยการตรวจสอบ OEE เมื่อเวลาผ่านไป ผู้ผลิตสามารถระบุแนวโน้ม และปรับปรุงกระบวนการผลิตของตนได้อย่างต่อเนื่อง สิ่งนี้สามารถนำไปสู่การปรับปรุงประสิทธิภาพการผลิต คุณภาพ และประสิทธิภาพการผลิตอย่างต่อเนื่อง
Quick MES รับรู้ต้นทุนการผลิตแบบอย่าง OEE แบบ Real Time
Quick MES ออกแบบมาเพื่อโรงงานอุตสาหกรรมที่ต้องการเพิ่มประสิทธิภาพการแข่งขัน รับรู้ต้นทุนการผลิตแบบ Real Time เช่น OEE Report, Scrap Report, Breakdown Report เป็นต้น ข้อมูลสถานะการผลิตจาก Machines จะส่งตรงไปยังระบบ ERP ที่คุณมีอยู่แล้วให้โดยอัตโนมัติแบบไร้รอยต่อตามข้อกำหนดของ ISA-95 ซึ่งข้อกำหนด ISA-95 จะทำให้มั่นใจได้ว่าโครงการบูรณาการระหว่างระบบ ERP และ MES ที่เกี่ยวข้องกับผู้คนจำนวนมากจะเป็นไปอย่างมีประสิทธิภาพ
MES แสดงผลการทำงาน 3 ด้าน ที่อัปเดตเป็นวินาที
นอกจากติดตามและแสดงผลสถานะการผลิตแบบเรียลไทม์แล้ว ระหว่างการผลิต MES ยังแสดงผลการทำงาน 3 ด้าน ที่อัปเดตเป็นวินาที คือ
ด้านประสิทธิภาพการทำงาน หรือ Availability (A)
หน้าจอจะแสดงให้เห็นแถบสีสถานะการทำงาน โดยสีเขียวคือช่วงเวลาที่เครื่องจักรทำงาน และสีส้มคือช่วงเวลาที่เครื่องจักรหยุดทำงาน การแสดงผลนี้จะทำให้เห็นว่าตลอดระยะเวลาทำงาน 8-9 ชั่วโมง เจ้าหน้าผู้ควบคุมที่อยู่ที่หน้างานหรือไม่, เครื่องจักรมีการทำงานจริงๆ กี่ชั่วโมง และยังบ่งบอกถึงประสิทธิภาพของเครื่องจักร หากเครื่องจักรหยุดทำงานนาน ๆ บ่อย ๆ อาจเป็นสัญญาณว่าเครื่องจักรเริ่มมีปัญหา
ด้านจำนวนชิ้นงานที่ผลิตได้ต่อระยะเวลาการผลิต หรือ Performance (P)
ระบบ MES จะคำนวณค่า P ว่าในแต่ละรอบการผลิตจะต้องผลิตชิ้นงานได้กี่ชิ้น และการผลิตจริงสามารถผลิตได้กี่ชิ้น เป็นไปตามที่ประเมินไว้หรือไม่ หากไม่เป็นไปตามที่ประเมิน หัวหน้างาน สามารถนำข้อมูลมาปรับแผนการผลิตได้ทันที เพื่อให้ได้จำนวนชิ้นงานตามที่วางแผน
ด้านคุณภาพ หรือ Quality (Q)
ระบบ MES จะแสดงผลการผลิตตลอดเวลาว่ามีผลงานที่ใช้ได้กี่ชิ้น และผลงานที่เสียกี่ชิ้น จะต้องผลิตเพิ่ม หรือ ต้องแก้ปัญหาอะไรบ้าง เพื่อให้ได้ผลงานเพียงพอตามออร์เดอร์ของลูกค้า
Quick Suggest
หากสนใจเรียนรู้เพิ่มเติม ขอแนะนำบทความ
สรุป
OEE ( Overall Equipment Effectiveness ) นับว่าเป็นดัชนีที่สำคัญต่อโรงงานอุตสาหกรรมเป็นอย่างมาก ทุกโรงงานควรนำไปประเมินประสิทธิภาพของการผลิตอย่างเป็นประจำ เพื่อให้มองเห็นภาพรวมของการผลิตว่าในตอนนี้มีคุณภาพมากน้อยเพียงใด สามารถแยกย่อยการตรวจสอบออกมาให้ละเอียดมากยิ่งขึ้น โดยการแบ่งการตรวจสอบให้ย่อยเล็กลงมากยิ่งขึ้น จากการตรวจสอบทั้งไลน์ผลิต อาจเปลี่ยนมาตรวจสอบแค่เครื่องจักรเครื่องเดียว ยิ่งการตรวจสอบแคบมากเท่าไหร่ ก็ช่วยให้มองเห็นภาพรวมของกระบวนการผลิตมากเท่านั้น และที่สำคัญคือการจดบันทึกจะต้องเป็นข้อมูลที่แม่นยำมากที่สุด มิฉะนั้นอาจทำให้การประเมินประสิทธิภาพได้ตัวเลขที่ผิดเพี้ยนไปจากเดิมอย่างแน่นอน
ก้าวเข้าสู่ Industry 4.0
ดูผลิตภัณฑ์ที่เกี่ยวข้องได้ที่นี่